As industries increasingly embrace digital transformation, the concept of digital twins has emerged in sectors such as defence and aviation. A digital twin is a virtual representation of a physical asset, system, or process that is .updated in real-time with data from the physical counterpart. Building on this technology, virtual prototyping — the creation of digital replicas of machines and systems — revolutionizes the design and development process in aerospace.
Engineers can craft digital models of machines and systems, testing and refining them in a virtual space before building anything physically. This process makes it easier to identify problems early on and improve performance. In the shift to digitalization, virtual prototyping is an essential tool that boosts efficiency, cuts costs, and helps the aerospace industry to overcome the challenges of designing advanced and complex modules. Let’s look at how virtual prototyping is revolutionizing aerospace development, with examples that highlight its practical applications.
Improving Communication Across Specialized Teams:
Aerospace projects involve teams with varied expertise, from avionics to structural engineering. Communication between these experts is critical, especially when design changes are necessary. Virtual prototyping allows teams to view and interact with a shared digital model, making it easier to discuss modifications and understand their implications.
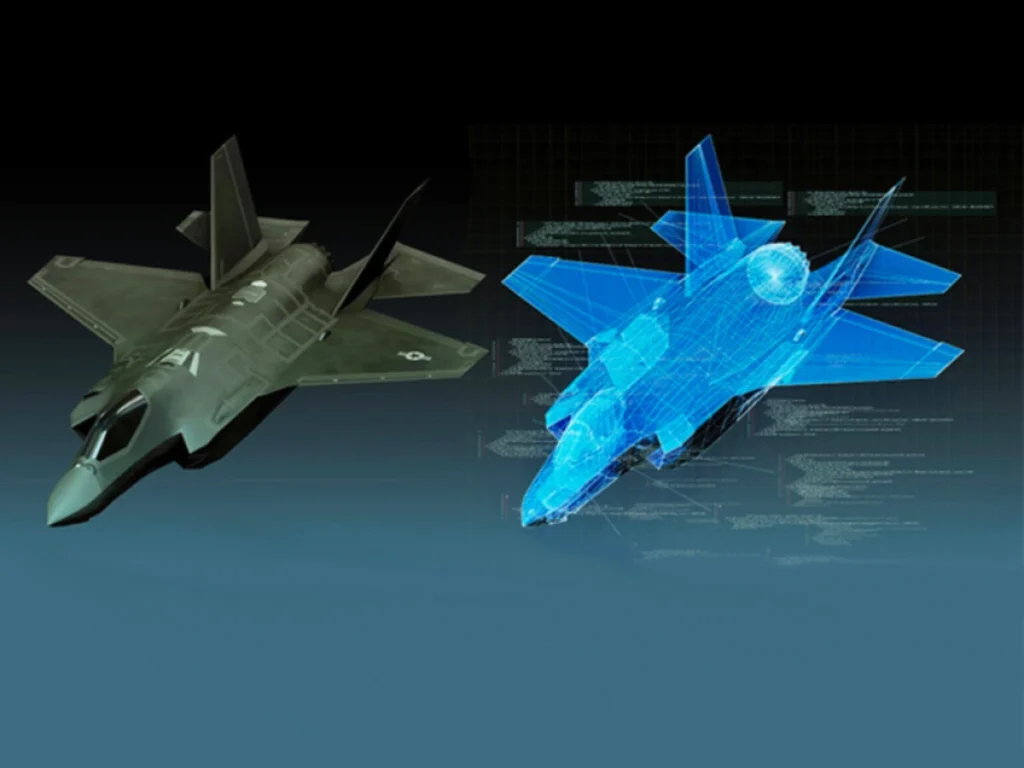
In Lockheed Martin’s F-35 program, virtual prototyping has enabled global collaboration. Engineers in different locations can access the same digital model, allowing them to see and discuss design adjustments in real-time. This improved communication reduces misunderstandings and aligns the entire team, helping to avoid delays and costly mistakes.
Accelerating Development through Agile Prototyping:
Agile development, traditionally used in software, is now achievable in hardware thanks to virtual prototyping. With digital models, aerospace teams can quickly make and test design adjustments, speeding up the iteration process.
Raytheon Technologies uses virtual prototypes to refine radar and missile designs. Digital testing allows Raytheon engineers to make changes without waiting for physical prototypes, significantly reducing the development timeline. By supporting rapid adjustments, virtual prototyping helps companies bring new innovations to market faster.
Reducing Material Waste and Production Costs:
Building physical prototypes requires expensive materials and complex manufacturing processes. Mistakes discovered late in development can lead to wasted resources and additional costs. Virtual prototyping addresses this by enabling early detection of design flaws in a digital model, so corrections are made before physical production begins.
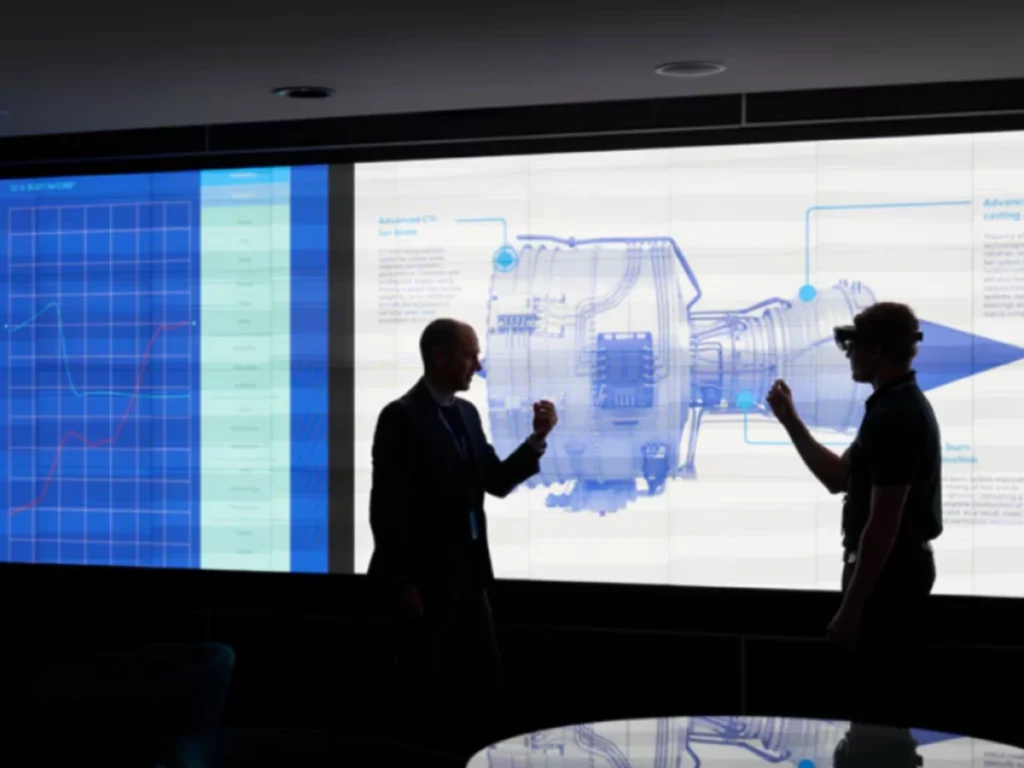
Rolls-Royce uses virtual prototyping to develop its UltraFan jet engine. By simulating airflow, temperature tolerances, and stress points digitally, the engineering team was able to optimize the design early on. This approach reduced material waste and saved both time and resources, allowing Rolls-Royce to proceed with a more efficient design when building the physical prototype.
Streamlining System Integration with Virtual Commissioning:
Integrating complex systems like robotic assembly lines for aircraft parts can be challenging and time intensive. Virtual commissioning uses digital twins to simulate and test how different systems will work together, helping to catch integration issues before implementation.
Siemens uses virtual commissioning for aerospace manufacturing, setting up and testing entire assembly lines in a virtual environment. By doing so, Siemens can identify and resolve potential issues beforehand, which minimizes downtime and reduces costs during actual production. Virtual commissioning allows aerospace companies to make integration smoother and more efficient.
Testing in Extreme Conditions with Virtual Models:
In aerospace, systems must operate reliably in extreme environments. Physical testing for conditions like extreme heat, radiation, or low gravity can be costly and logistically challenging. Virtual prototyping allows engineers to simulate these conditions digitally and test system resilience without building multiple prototypes.
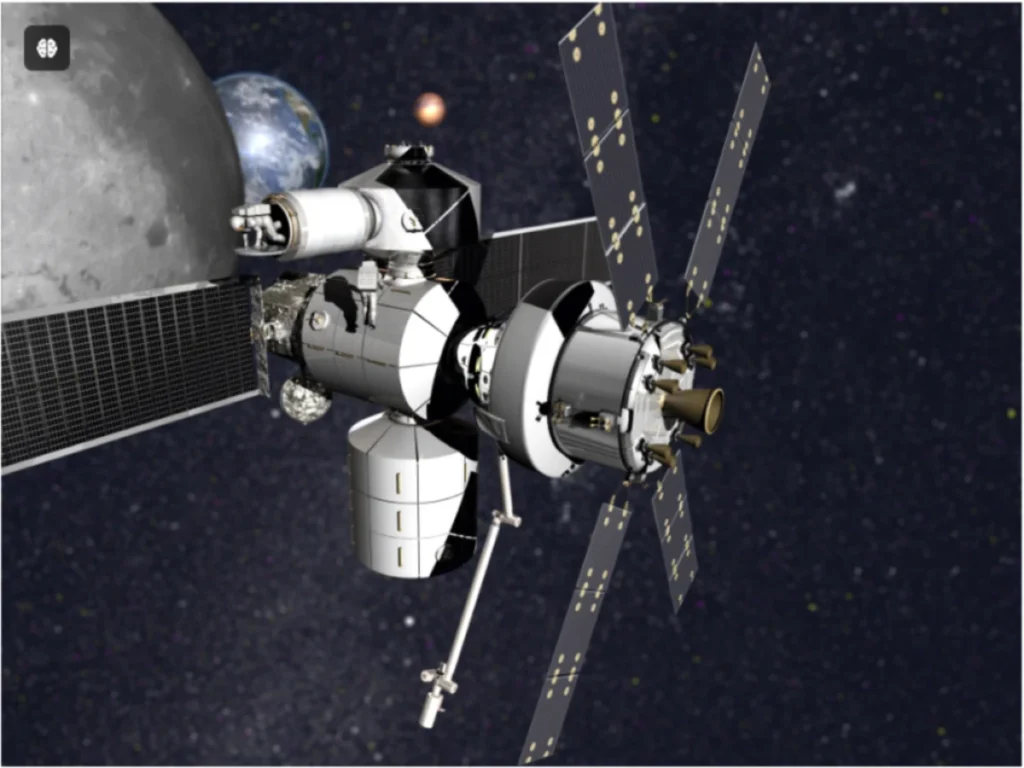
NASA uses virtual prototyping to prepare spacecraft components for space missions. By simulating harsh environments digitally, engineers can identify design improvements early in the process. This kind of testing helps minimize risk and increase performance before physical testing even begins.
Virtual prototyping is transforming aerospace design and development. It enhances team communication, enables faster and more agile cycles, reduces material waste, simplifies system integration, supports extreme-condition testing, and helps predict maintenance needs. For aerospace companies and investors, virtual prototyping offers a clear advantage, making it easier to innovate efficiently while saving resources. As the industry moves toward digitalization, virtual prototyping will remain at the forefront, helping engineers bring the next generation of aerospace technology to life with precision and confidence.
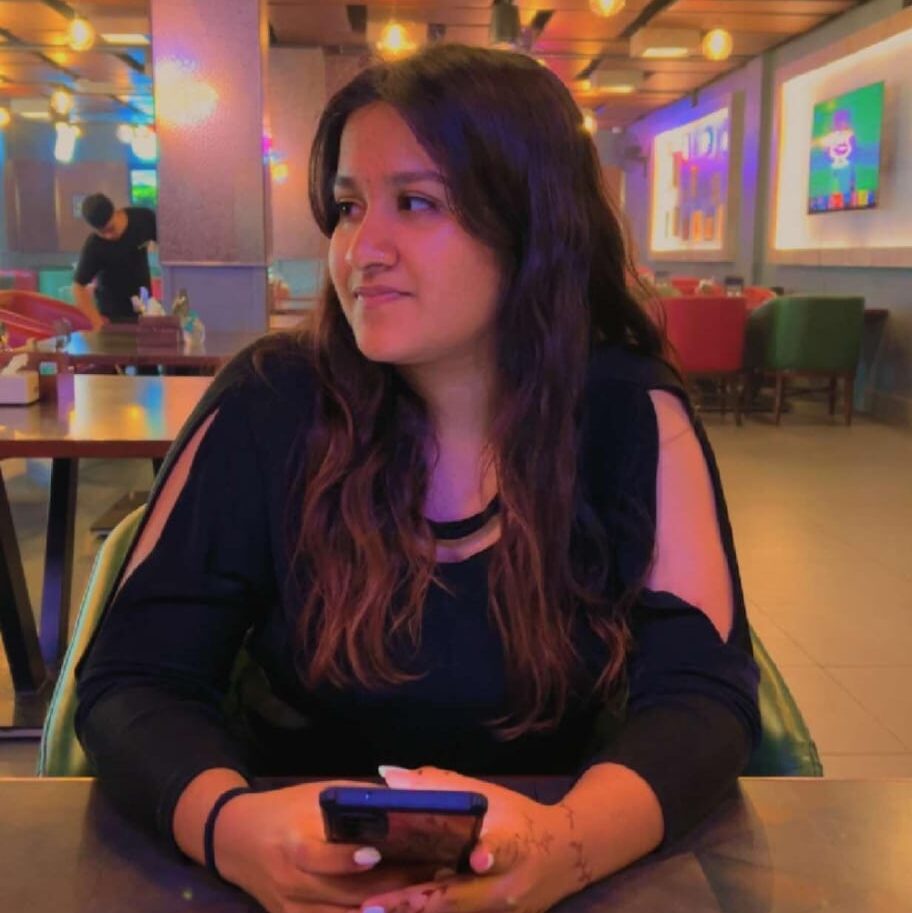
About the Author
Jahnavi Naganand
An ambitious aerospace engineering undergraduate with a passion for propulsion systems, aircraft design, and composite materials. Enthusiastic about developing digital solutions to optimize aerospace systems for aviation and defense, she also enjoys photography and music.
Leave A Comment